BISON has provided more than 6,000 high performance mechanical anchors for the installation of the electrical services and public address (PA) system in one of the country’s most high profile new road tunnel projects.
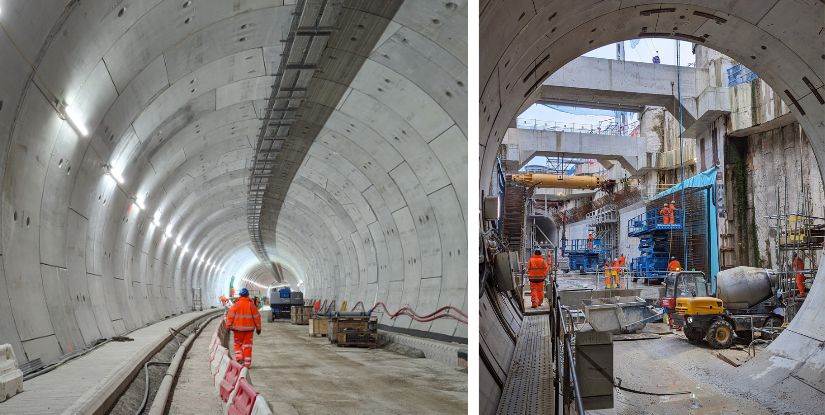
EJOT and LIEBIG branded HCR (high corrosion resistance) anchors have been supplied for the major civil engineering project by BISON, in response to the contractors approach to help them with a product that met the required high performance specifications for road tunnels.
Beneath one of the UK’s most significant waterways a new road tunnel has been constructed to alleviate the usage pressure on existing tunnels, and to meet the demanding performance specification required for the highly corrosive environment, the anchors needed to be an exceptionally high grade of stainless steel. At the same time, BISON were tasked to ensure the solution would enable the main contractor to keep the project on track and on budget by avoiding the lengthy lead times and high unit costs often associated with such products.
As one of the world’s leading manufacturers of heavy duty anchors, through-bolts and concrete screws, which are used extensively in many different types of construction projects, BISON was able to meet the requirements of the brief with maximum efficiency, by engaging EJOT UK. They recommended two products from their extensive portfolio – the EJOT BA-E Plus HCR through-bolt manufactured in 1.4529 high corrosion resistance stainless steel, and the LIEBIG Superplus BLS-P self-undercutting heavy duty expansion anchor manufactured in A4 stainless steel.
The BA-E Plus 10/10 HCR through-bolt anchors specified have been used to securely attach the bracketry for the electrical system trays throughout the tunnel development. EJOT was able to provide a bespoke version of this versatile 120-minute fire-rated through-bolt which features an additional washer to offset the brackets from the tunnel wall and prevent moisture collecting. A special tool was also supplied by EJOT to enable easier overhead installation of the anchors.
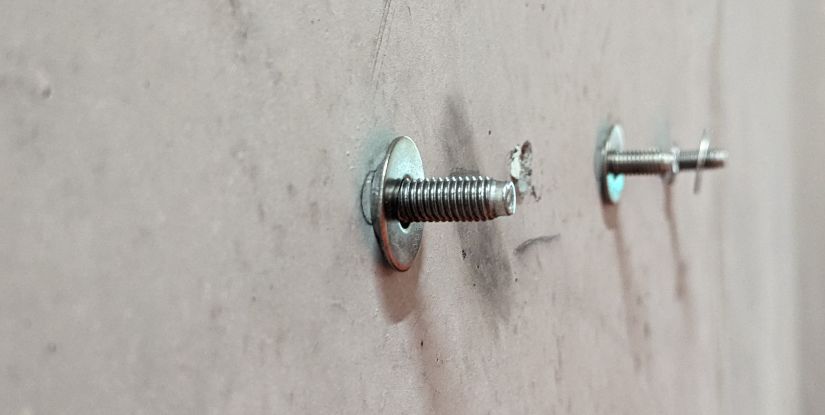
Bespoke LIEBIG Superplus BLS-P anchors in two different lengths were specified for use in stand-off applications that included speakers and other components associated with the tunnel’s PA system. These anchors met a slightly different brief in that they were also required to demonstrate a high level of vibration resistance resulting from vehicle flow through the tunnel. The PA system bracketry then utilised the anchors two lengths to accommodate the size and shape of the speakers in the context of the tunnel’s curved walls.
Bill Browning, Business Development Director at BISON UK, said: “We were thrilled to be able to provide the main contractor with an anchoring solution that ticked all the boxes for this prestigious project. The combination of exhaust emissions from vehicles and the moisture laden air, given the close proximity to the water, demanded HCR anchors, and it was clear that the EJOT and LIEBIG products recommended by EJOT’s anchoring specialist consultants would achieve the performance specification.
“But it was also imperative that these could be provided within relatively short lead times and to a strictly controlled budget, and here the EJOT package met the brief without compromise. The EJOT team provided all the technical data necessary to demonstrate that both the BA-E Plus and Superplus BLS products would perform in-situ, with the added assurance of European Technical Assessments (ETAs), and enable fast, efficient installation.
“And because of the way their business is set-up, they could offer the flexibility we required to accommodate the bespoke anchor design and smaller volumes involved in this project.”
Both the anchors supplied by EJOT for this tunnel project are designed for use in cracked and non-cracked concrete where only a relatively shallow embedment depth is possible. They provide medium to high load capacity in a diverse range of applications including nuclear facilities and industrial plants.
EJOT UK’s Business Development Manager, Gary Robson, added: “From the moment BISON UK first approached us to help on this project, it was obvious that we could help given the breadth and depth of our anchoring range and our technical expertise locally and internationally.
“Once the products were identified, we conducted pull-out tests, installation trials and tool-box-talks on-site to confirm their suitability and supported the installers to get the optimum results for the client. Turnaround of all bespoke products was less than ten days at our Yorkshire manufacturing facility near Leeds.”
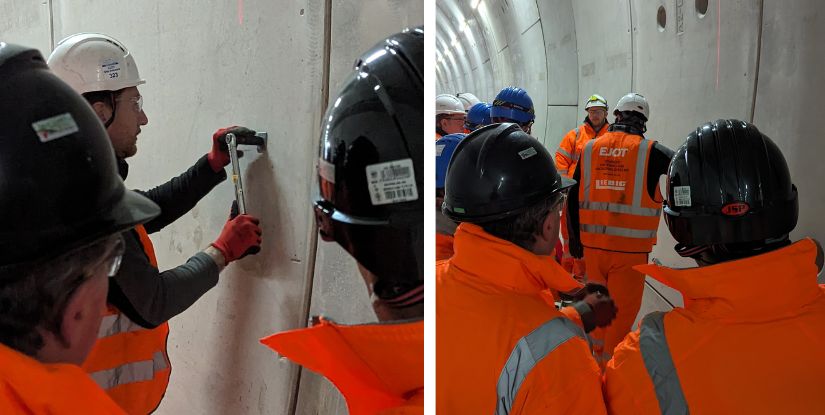
Get in contact on 01329 222 345 or sales@bisonuk.com to see what value Bison can bring your infrastructure project.